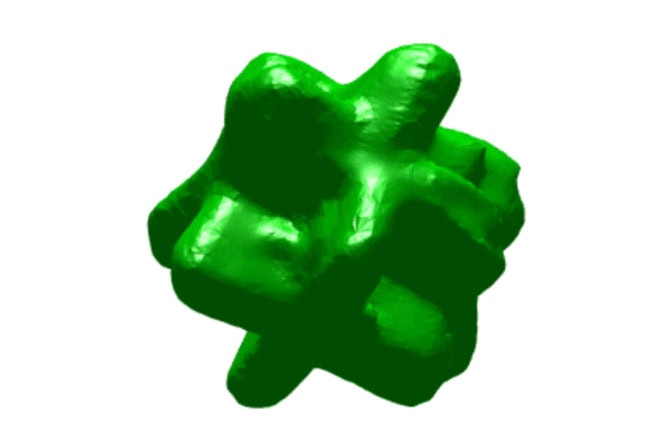
First 3D visualization of an aluminum nanocomposite for the auto industry
The lightweight material could extend EV range or fuel efficiency once its microstructure is understood.
The lightweight material could extend EV range or fuel efficiency once its microstructure is understood.
Experts
Manufacturing cars with strong, lightweight aluminum alloys rather than steel could improve fuel efficiency and extend electric vehicle range, but the material’s instability at high temperatures has held the alloys back from widespread adoption.
Creating tiny, reinforcing particles of titanium carbide (TiC) directly inside of molten aluminum results in a stronger, more temperature resistant aluminum-based material called a metal matrix nanocomposite.
Up to this point, researchers have not understood how these nanoparticles form, or how they interact with other features in the microstructure, hindering production of the material on an industrial scale.
University of Michigan researchers have used a unique high-resolution, 3D x-ray technique to provide a first glimpse into how nanoparticles form, where they are located and how they facilitate further solidification of the molten metal. A paper on the work will be published in the September edition of Acta Materialia.
Explore the forefront of digital engineering
at Michigan Engineering
“Most metals start their lifetimes in the liquid state. How they convert from liquid to solid will ultimately determine their microstructures, and hence, their properties and applications,” said Ashwin Shahani, an associate professor of materials science and engineering and chemical engineering at U-M and co-corresponding author of the study.
“The study enabled us to understand exactly how the nanoparticles interact with secondary phases in casting, which has been a major challenge for the past half-century.”
As nanoparticles are less than 100 nanometers, one ten-thousandth of a millimeter, the researchers used a powerful imaging technique called synchrotron-based x-ray nanotomography to visualize metal microstructure nondestructively in 3D—a feat not possible with conventional imaging approaches.
To obtain the visualizations, the researchers created an aluminum composite reinforced with titanium carbide (TiC). That involved a flux-assisted reaction in which a mixture of carbon powder and titanium-bearing salt was reacted with an aluminum melt.
3D reconstructions revealed an unexpected diversity of titanium aluminide (Al3Ti) intermetallic structures, including one that formed directly on TiC nanoparticles larger than 200 nm in diameter. In that case, the Al3Ti crystals grew into an unusual orthogonal plate structure. Meanwhile, the TiC nanoparticles smaller than the 200 nanometer threshold split the Al3Ti intermetallic plates during solidification, forming branched structures.
In addition to imaging, the researchers used phase-field simulations to fill in spatiotemporal “gaps” in the experiments and propose a mechanism for microstructure formation.
“We now have evidence that the nanoparticles form well before the intermetallics, and not the other way around, which has important implications regarding the nucleation of the nanoparticles in the first place,” said Shahani.
With these results in hand, industry partners can now guide TiC and Al3Ti formation when manufacturing aluminum composites on a large scale—adjusting solidification pathways or alloy chemistries to achieve the desired microstructure and its associated properties.
“We have known for a long time that nano-sized particles could improve the performance of metal matrix composites, but the materials could not be produced at scale. We now understand the formation mechanisms that will enable our industry partners to optimize the process for lightweighting applications,” said Alan Taub, a Robert H. Lurie Professor of Engineering and director of the Electric Vehicle Center at U-M and co-corresponding author of the study.
Taub is also a professor of materials science and engineering, mechanical engineering and macromolecular science and engineering.
This research was funded by the National Science Foundation (grant no. 1762657).
Synchrotron-based x-ray nanotomography was performed at the National Synchrotron Light Source II at Brookhaven National Laboratory. Further characterization was done at the Michigan Center for Materials Characterization.