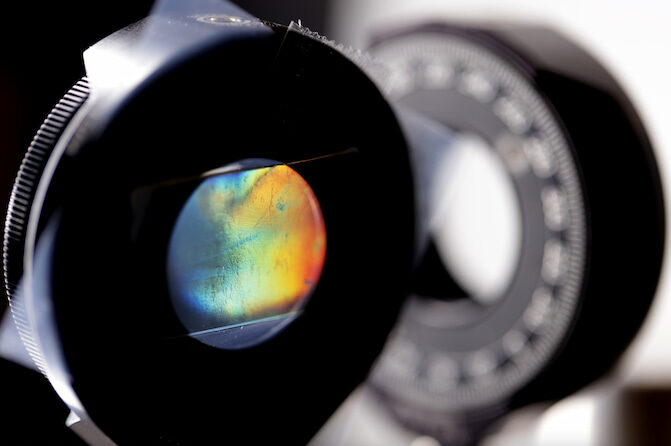
Nanoscale engineering brings light-twisting materials to more extreme settings
New manufacturing method builds tougher materials that were previously considered useless for twisting light into more robust optical devices.
New manufacturing method builds tougher materials that were previously considered useless for twisting light into more robust optical devices.
Experts
Irving Langmuir Distinguished University Professor of Chemical Sciences and Engineering
Joseph B. and Florence V. Cejka Professor of Engineering
Professor of Chemical Engineering
Professor of Macromolecular Science and Engineering
Imaging the hot turbulence of aircraft propulsion systems may now be possible with sturdy sheets of composite materials that twist light beams, according to research led by the University of Michigan and Air Force Research Laboratory.
The sheets were produced with a new manufacturing method that opens possibilities beyond aircraft design, as it enables new classes of materials to be used in polarization optics. While the team demonstrated high temperature tolerance, new mechanical, electrical and physical properties are expected to emerge as well—with potential applications in energy, sensors for vehicles and robots, and space exploration.
“Combining multiple functionalities into 2D materials opens up a world of possibilities,” said Dhriti Nepal, senior research materials engineer at the Air Force Research Laboratory and a co-corresponding author of the study published recently in Nature.
“Think of a butterfly’s wings, which allow it to fly, regulate temperature, and reflect light to produce specific colors for attracting mates and avoiding predators. This technique provides new design opportunities for creating multifunctional devices capable of anything one can imagine.”
The key is arranging nanomaterials that don’t twist light on their own onto layers that turn light waves into either left- or right-handed spirals, known as circular polarizations. In the aircraft example, turbulence created by the engine spins the light, which is then filtered through the material for imaging. Today, devices like LCD screens and thermochromic paints already control the twist and orientation of light waves using liquid crystals, but they melt not far above ambient temperatures.
“There could be situations in which you want to twist light outside the normal operating temperatures of liquid crystals. Now, we can make light-polarizing devices for those kinds of settings,” said Nicholas Kotov, the Irving Langmuir Distinguished University Professor of Chemical Sciences and Engineering at U-M and lead author of the study.
The new material can twist light at 250 degrees Celsius, and through the imaging of turbulence in aircraft engines and other applications, it could enable aerospace engineers to improve designs for better aircraft flight performance.
“Future aerospace systems continue to push the edge of technical feasibility. These low-cost optical materials afford modularity, which is crucial for optimizing solutions for a broad range of future technologies,” said Richard Vaia, materials and manufacturing chief scientist at the Air Force Research Laboratory and a corresponding author of the study.
To make the materials, the researchers put microscopic grooves into a plastic sheet and covered it with several layers of tiny, flat particles with a diameter 10,000 times smaller than a millimeter. These particles were held in place with alternating layers of a molecular adhesive, and they could be made from any material that can be made into flat nanoparticles. For their heat-tolerant materials, the researchers used ceramic-like materials called MXenes.
As light moves through the material, it divides into two beams, one with horizontally oscillating waves and another with vertically oscillating waves. The vertical waves pass through faster than the horizontal waves. As a result, the waves exit out of phase and appear as a spiral of light. The angle of the grooves determines the direction in which the light spirals, and layers of silver nanowires can help ensure the light spirals solely to the left or right.
“Our calculations suggest that the optical properties didn’t come from the nanoplates themselves, but from their orientation on the grooves caused by our fabrication process,” said André Farias de Moura, associate professor of chemistry at the Federal University of São Carlos and a co-corresponding author of the study.
The research was funded by the National Science Foundation Science and Technology Center for Complex Particle Systems, U.S. Department of Defense, U.S. Office of Naval Research, U.S. Air Force Office of Scientific Research, Brazil’s National Council for Scientific and Technological Development, as well as the São Paulo Research Foundation. The materials were studied at the Michigan Center for Materials Characterization.
Felippe Colombari from the Brazilian Biorenewables National Laboratory also contributed to the study. Nicholas Kotov is also the Joseph B. and Florence V. Cejka Professor of Engineering and a professor of macromolecular science and engineering.
Kotov filed a patent with the help of Innovation Partnerships at U-M, and his company Photon Semantics LLC, a U-M startup, is planning to license the technology. Kotov and the University of Michigan have a financial interest in Photon Semantics LLC.