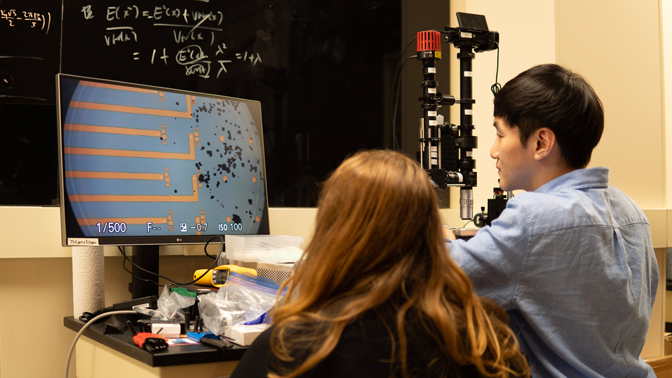
Cracking in lithium-ion batteries speeds up electric vehicle charging
Cracks in predominant lithium-ion electrodes shorten battery lifespans, but a neuroscience-inspired technique shows that they have an upside.
Cracks in predominant lithium-ion electrodes shorten battery lifespans, but a neuroscience-inspired technique shows that they have an upside.
Rather than being solely detrimental, cracks in the positive electrode of lithium-ion batteries reduce battery charge time, research done at the University of Michigan shows.
This runs counter to the view of many electric vehicle manufacturers, who try to minimize cracking because it decreases battery longevity.
“Many companies are interested in making ‘million-mile’ batteries using particles that do not crack. Unfortunately, if the cracks are removed, the battery particles won’t be able to charge quickly without the extra surface area from those cracks,” said Yiyang Li, an assistant professor in materials science and engineering and corresponding author of the study published open-access in Energy and Environmental Sciences.
“On a road trip, we don’t want to wait five hours for a car to charge. We want to charge within 15 or 30 minutes,” he added.
The team believes the findings apply to more than half of all electric vehicle batteries, in which the positive electrode—or cathode—is composed of trillions of microscopic particles made of either lithium nickel manganese cobalt oxide or lithium nickel cobalt aluminum oxide. Theoretically, the speed at which the cathode charges comes down to the particles’ surface-to-volume ratio. Smaller particles should charge faster than larger particles because they have a higher surface area relative to volume, so the lithium ions have shorter distances to diffuse through them.
However, conventional methods couldn’t directly measure the charging properties of individual cathode particles, only the average for all the particles that make up the battery’s cathode. That limitation means the widely accepted relationship between charging speed and cathode particle size was merely an assumption.
“We find that the cathode particles are cracked and have more active surfaces to take in lithium ions—not just on their outer surface, but inside the particle cracks,” said Jinhong Min, a doctoral student in materials science and engineering working in Li’s lab. “Battery scientists know that the cracking occurs but have not measured how such cracking affects the charging speed.”
Measuring the charging speed of individual cathode particles was key to discovering the upside to cracking cathodes, which Li and Min accomplished by inserting the particles into a device that is typically used by neuroscientists to study how individual brain cells transmit electrical signals.
“Back when I was in graduate school, a colleague studying neuroscience showed me these arrays that they used to study individual neurons. I wondered if we can also use them to study battery particles, which are similar in size to neurons,” said Li.
Each array is a custom-designed, two-by-two centimeter chip with up to 100 microelectrodes. After scattering some cathode particles in the center of the chip, Min moved single particles onto their own electrodes on the array using a needle around 70 times thinner than a human hair. Once the particles were in place, Min could simultaneously charge and discharge up to four individual particles at a time on the array and measured 21 particles in this particular study.
“Such an innovative approach allows statistical evaluation of active cathode materials with robust quantitative information, which was previously not possible with other methods,” said Shirley Meng, a professor of molecular engineering at the University of Chicago and Chief Scientist of Argonne National Laboratory’s Collaborative Center for Energy Storage Science, who was not involved in the study.
The experiment revealed that the cathode particles’ charging speeds did not depend on their size. Li and Min think that the most likely explanation for this unexpected behavior is that larger particles actually behave like a collection of smaller particles when they crack. Another possibility is that the lithium ions move very quickly in the grain boundaries—the tiny spaces between the nanoscale crystals comprising the cathode particle. Li thinks this is unlikely unless the battery’s electrolyte—the liquid medium in which the lithium ions move—penetrates these boundaries, forming cracks.
The benefits of cracked materials are important to consider when designing long-lived batteries with single-crystal particles that don’t crack. To charge quickly, these particles may need to be smaller than today’s cracking cathode particles. The alternative is to make single-crystal cathodes with different materials that can move lithium faster, but those materials could be limited by the supply of necessary metals or have lower energy densities, said Li.
The research was funded by LG Energy Solution, Battery Innovation Contest and the University of Michigan College of Engineering. Other contributors included Lindsay Gubow, a former master’s student in materials science and engineering, Riley Hargrave, an undergraduate in mechanical engineering graduating next year, and Jason Siegel, a research scientist in mechanical engineering.
The device was built in the Lurie Nanofabrication Facility and studied at the Michigan Center for Materials Characterization.