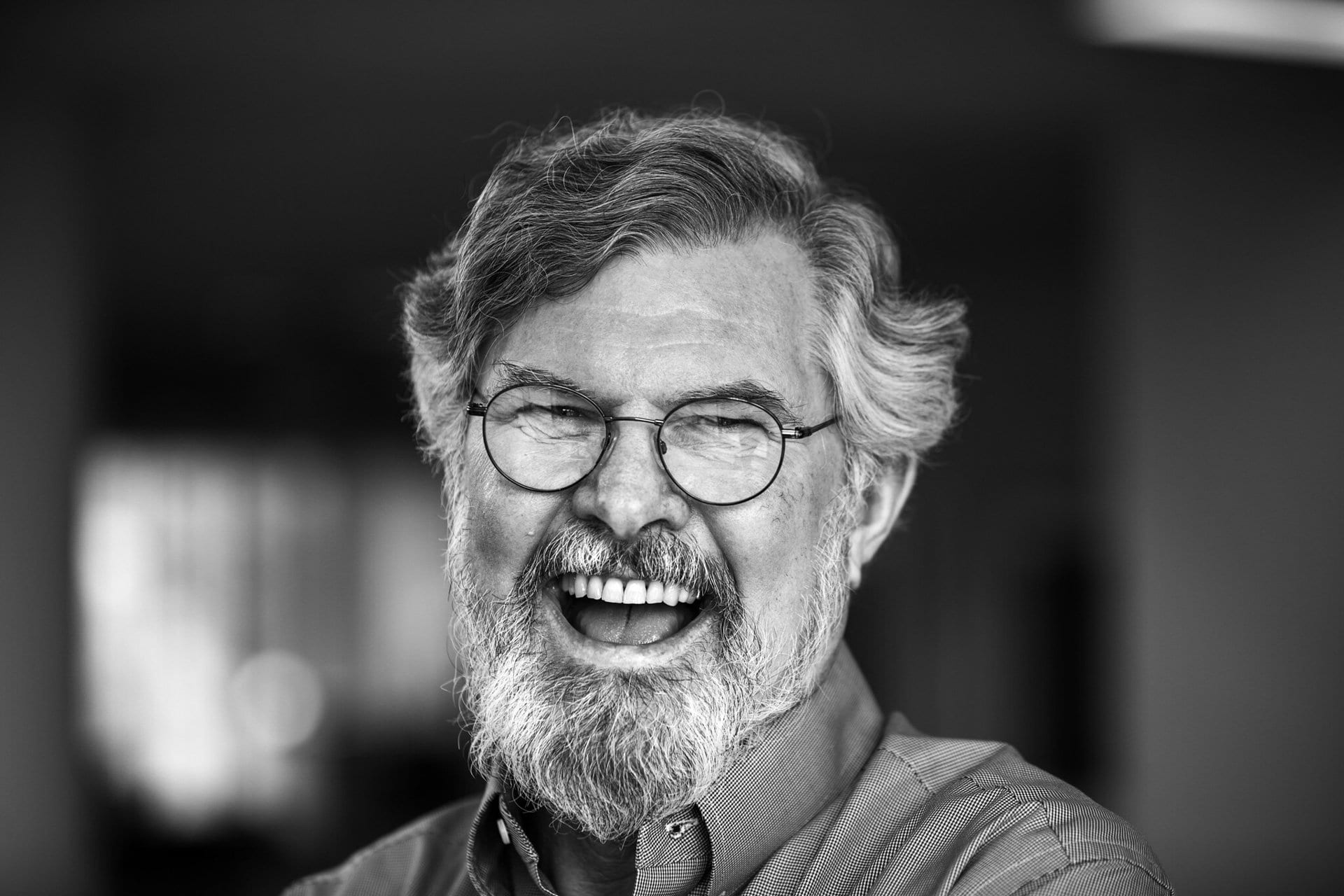
Advancing computational understanding of metallic materials
NAE profile: John Allison, mechanical engineering
NAE profile: John Allison, mechanical engineering
Get to know Michigan Engineering’s National Academy of Engineering members.
John Allison was elected for his research in metallurgy, particularly in light metals like aluminum, magnesium, and titanium. He has been a trailblazer in the field of Integrated Computational Materials Engineering (ICME), which aims at minimizing the time and expense of new materials and process development.
At Ford Motor Company, he developed models to address metal fatigue, enhancing powertrain castings. Now, as the head of the PRISM Center, Allison oversees open-source software developments and magnesium alloy research to aid in lightweight materials development.
For these achievements, John Allison was elected to the National Academy of Engineering in 2011. See the NAE citation.
More on John Allison
Allison: I grew up in a small town in Missouri, a boyhood home of Walt Disney, so a little railroad town out in farm country. I was interested in science and math and never really had traveled much beyond that. I had a guidance counselor who had been to the Air Force Academy and said you ought to think about [the Air Force]. And so I said, okay, that sounds interesting, and I went to the Air Force Academy in Colorado. After four years there I got a degree in engineering mechanics. But that also had a materials minor, and I learned about this thing called Microstructure. I just found it fascinating that you could change how a metal behaved.
Allison: At Ford, I got more intrigued by how you get parts on cars. I worked for a long time on things like titanium-connecting rods and aluminum piston or aluminum-connecting rods and different things. And I realized it was really tough to get advanced materials into the auto industry.
Then I got into this cast aluminum. We were watching all these cast aluminum products, and I realized there was some good fundamental science that we really needed to know more about it. They were breaking all the time and I thought I could contribute to that. And that led to this whole thing about linking.
The trick was we had all these manufacturing simulation codes for casting modeling. We had really great codes for doing fatigue analysis, but we didn’t understand how manufacturing string history affected the properties that we put into that fatigue analysis. So that was the real key missing link. So I convinced management to give me some good funding and we built a team to figure out how to fill that missing gap. It saved Ford lots of money and really launched these new products very quickly. So that was a very, very exciting time. And that group still exists at Ford.
Allison: I’ve been an adjunct at Michigan, so I knew a little bit about the position, but I’d never taught, I’d never done fundraising, so on and so forth. Teamwork was a big thing for me at Ford. I really love collaboration. So coming here to Michigan, I thought I’ll just use some of those same skills. But learning how to collaborate with academics is a different beast than collaborating with engineers in a company.
It was a very difficult transition for me, not because I didn’t enjoy the science and the teaching and the students, but it was learning the new skills. Teaching was something I’d never done. I needed to master that skill, which was not trivial with multitasking, fundraising, service, etc. I loved working with students. I had to learn how to mentor them to be successful. There were some skills that I had to learn there. There’s a thing called the imposter syndrome that they think they’re not as good as they are. So working them through it, recognizing that they’re in a mental space where they may not be really realizing their capabilities, and getting through that.
Allison: Typically with engineering products you assume that each time you manufacture something, it gives more or less the same result. But with additive 3D printing, every new process may be a little bit different because all the components are little powders that you’re melting that can all have different characteristics. So you have to really understand a lot more in detail because you don’t have the ability to test all those parts.
We’re trying to develop new ideas and methodologies for how to really validate that whole process. A big part of what I’m doing now is something called the PRISMS Center. We’re developing open source software and experiments to study the software and advance our knowledge. The PRISMS center is funded by the Department of Energy and they’re really focused on the fundamentals. So we’re trying to develop a capability for people to develop new alloys or new processes. One of the things we’re working on now is the ability to predict how a certain microstructure is farmable. Using these models, we’re able to start to understand how we might modify an alloy or how we might alter the steps in our manufacturing process to get to a more formidable alloy.
Quotes edited from interview transcript between John Allison and Marcin Szczepanski.