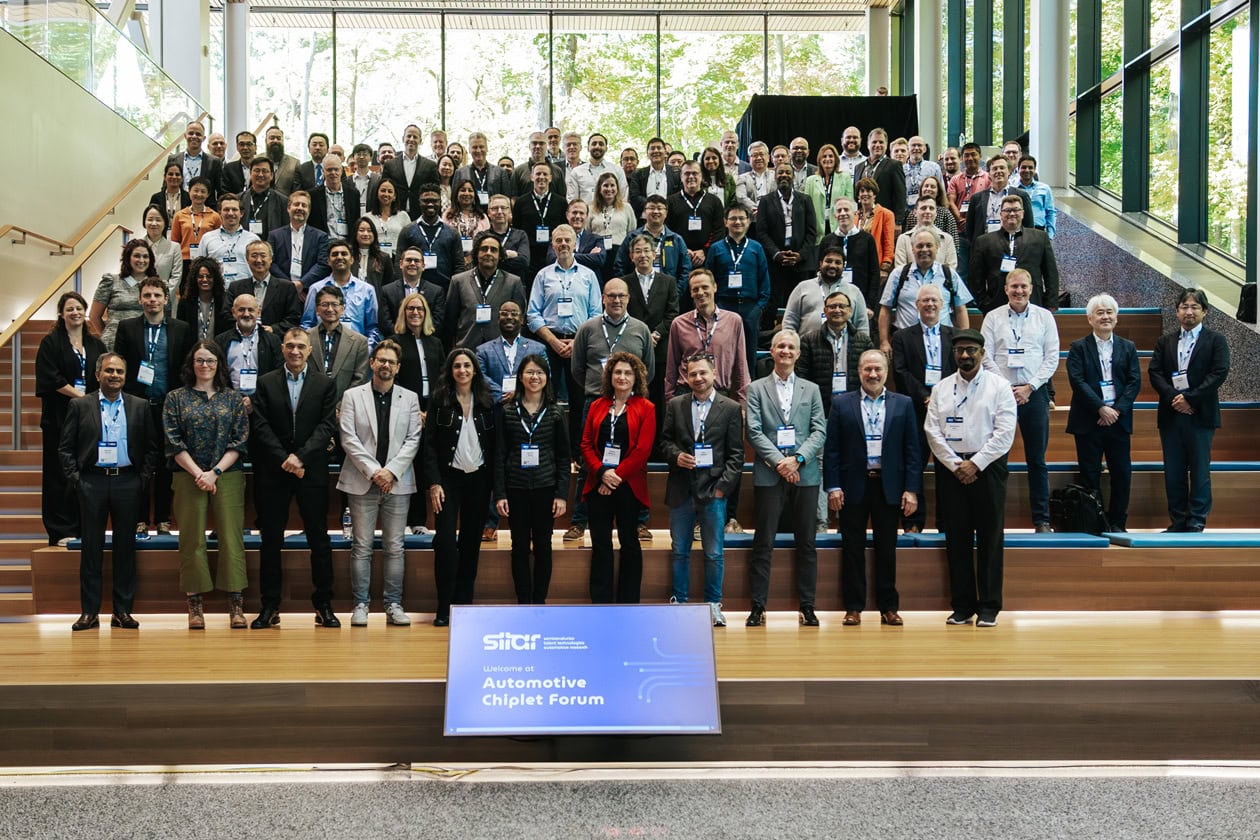
U-Michigan’s lead role in vital automotive semiconductor efforts
Through R&D, education, and international partnerships, Michigan Engineers are working to unleash the next wave of advancements in mobility.
Through R&D, education, and international partnerships, Michigan Engineers are working to unleash the next wave of advancements in mobility.
A new generation of semiconductor technologies is needed for the auto industry to unlock the full potential of autonomous and electric vehicles, and the University of Michigan is at the forefront of recent broad-based efforts to bridge this gap.
Last week, Michigan Engineering faculty members and some of its key infrastructure played prominent roles in several events in Ann Arbor that brought together leaders from the semiconductor and auto sectors to forge innovative ways forward.
On October 10 and 11, U-M researchers participated in the Automotive Chiplet Forum, hosted at the Michigan headquarters of semiconductor equipment firm KLA. The forum convened more than 130 experts from major automakers, Tier 1 and Tier 2 suppliers, along with microelectronics systems companies that support the automotive industry, including silicon design, manufacturing, testing and equipment firms.
Organized three times previously by semiconductor R&D hub imec, the forum was brought to the U.S. for the first time this year as part of the Michigan Semiconductor Talent and Technologies for Automotive Research, or mstar, initiative. Mstar (pronounced em-star) founding partners include U-M, imec, KLA, the Michigan Economic Development Corporation, Washtenaw Community College and General Motors. Mstar is the U.S. chapter of star, a global network that unites experts from the automotive and semiconductor industries to foster R&D collaboration, promote standardization, and support workforce development.
“The Automotive Chiplet Forum, or ACF, is built on imec’s legacy in semiconductor automotive technology, and we’re excited to bring this expertise to the U.S. market,” said Bart Plackle, imec’s VP automotive. “ACF aims to lead the charge as the automotive industry increasingly integrates semiconductor technologies for enhanced performance, safety, and connectivity.”
Forum participants also toured the U-M Battery Lab and Mcity Test Facility, the world’s first purpose-built test environment for automated and connected vehicles and technologies. Last week Mcity also hosted representatives and guests from Natcast, which operates the National Semiconductor Technology Center, a public-private consortium established by the CHIPS Act to address barriers in the domestic semiconductor industry.
“Automotive is the fastest growing segment in the semiconductor industry. The industry is accelerating its advancement towards autonomous mobility, which requires robust, and high-performance solutions with a minimal cost and energy profile. At U-M, we’re bringing together our deep expertise in both microelectronics and automotive to lead the charge in the development of these technologies and build a skilled workforce tailored to industry needs,” said Valeria Bertacco, the Mary Lou Dorf Collegiate Professor of Computer Science and Engineering and U-M vice provost for engaged learning. Bertacco gave a keynote address at the Automotive Chiplet Forum.
KLA has been working closely with the auto industry for around a decade.
“As we talked to automakers, we came to understand that their requirements for chips
are different than those for smartphone production or for data centers,” said Oreste
Donzella, executive vice president and chief strategy officer at KLA. “Zero defect is the
mantra because of strict standards for automotive quality and reliability. When you put
chips in a car and they’re submitted to harsh environments, even tiny latent defects can
cause them to fail.”
The company has developed new solutions that are customized for the auto industry to
screen chips for reliability issues. As chips increase in complexity, it becomes more and
more challenging to achieve zero-defect.
At the same time, increases in automated features and the push toward full autonomy have drastically increased the number and resolution of on-vehicle sensors, leading to torrents of data that must be processed in real time to analyze the vehicle’s context and develop autonomous decisions. Meanwhile, the ongoing transition to electric drivetrains limits a vehicle’s energy budget to its battery capacity.
“The automotive industry is going through a transformation driven by electrification, connectivity and autonomy. It’s turning vehicles into powerful computers on wheels,” Rahul Rithe, principal engineer at Rivian, said at the conference. “Autonomy performance is increasing substantially, but the amount of data and computing required grows exponentially. To fulfill such fast-paced computing demands, we need rapid hardware design cycles and massive efficiency gains to reduce power and compute cost. Enabling advances in autonomy requires us to bridge the gap between the pace of AI innovation and automotive hardware development.”
The semiconductor industry has been working on these challenges, Natcast visitors said.
“It’s a hard problem to solve,” Michael Sun, who leads the automotive business development unit at Taiwan-based TSMC, said while touring Mcity with Natcast.
“You’re essentially putting a supercomputer on a car. You need more sensors, more compute power, and that takes energy. It’s great to see people coming together to address these aspects. I’ve been working in this area for a long time, and I think there’s a lot of momentum right now. Semiconductors are cool again.”
The Mstar forum focused on chiplets, one potential solution to the technological hurdles.
In traditional integrated circuits, all the necessary components—central processing units, graphics processing units, memory, etc.—are printed on a single silicon die. These monolithic architectures are reaching their physical size limits in handling vehicles’ complexity and performance requirements, experts said. The larger and more complicated chips get, the more prone they are to defects and failures, which are especially dangerous in cars and trucks.
Chiplets are smaller, modular components that are optimized for particular functions and can be combined in custom ways to operate as a larger, more complex system. They could potentially enable the reliable high-performance computing in extreme environments that advanced automotive features require. They could also streamline chip design and manufacturing, making it possible for auto companies without deep semiconductor expertise to innovate in-house. Additionally, they would support a flexible, sustainable supply chain that can adapt to evolving industry needs. Forum speakers shared the vision of a standardized ecosystem that could accommodate specialized components from different vendors.
At the forum, imec announced that 10 companies have joined its new Automotive Chiplet Program, which aims to evaluate which chiplet architectures and packaging technologies are best suited for car manufacturers’ high-performance computing and strict safety requirements. Kurt Herremans, imec’s automotive program director, also described the organization’s mechanical test vehicle demonstrator that can measure how chiplets are performing, which is important because they could potentially deteriorate at different rates.
“We want to build a system that, if a failure happens, doesn’t topple over immediately, but can recover or turn off a core or bring on a new core without affecting the availability of the system to the user,” Herremans said.
Arm, the British semiconductor and software design company whose processors are ubiquitous in smartphones, has been engaging with industry on chiplets for several years in an effort to “encourage more plug-and-playability,” said John Kourentis, Arm’s director of automotive go-to-market.
“There are megatrends happening in our space that are causing disruption and opportunity as well,” Kourentis said. “The massive growth in ADAS (advanced driver assistance systems), coupled with significant advances in user experience and the expectation of passengers, as well as a significant shift in drivetrain to electrification. Bring all three of these things together and they result in a tremendous growth in software complexity. These challenges need us to build new partnerships and new business models to work in a different way than we’ve done.”
Through its Arm Chiplet System Architecture, the company is working with more than 50 partners on standardization.
“Monolithic dies are reaching their limit in terms of size and yield,” Kourentis said. “Today we’re seeing single-vendor chiplet systems that are tightly coupled together. The utopia is a multi-vendor marketplace where chiplets fit together like Lego bricks.”
Nicole Casal Moore
Communications & Public Engagement Director