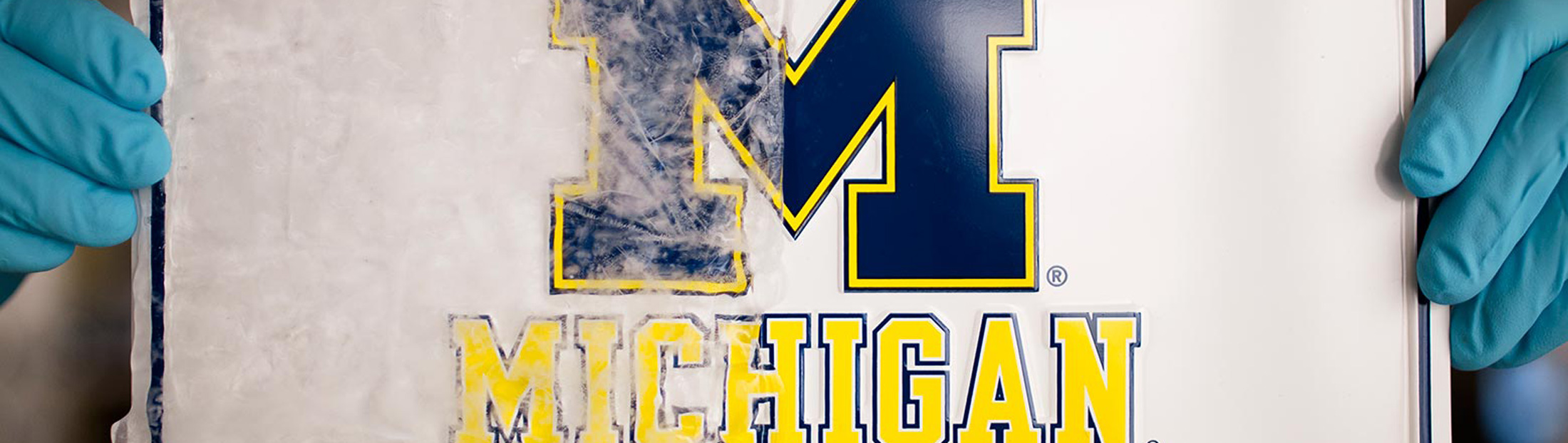
Excelling at repelling
A material science researcher’s drive to ice-, barnacle-, and kid-proof coatings
A material science researcher’s drive to ice-, barnacle-, and kid-proof coatings
Anish Tuteja has dedicated the better part of a decade to coatings that prevent things from sticking to other things. It’s an idea that sounds simple; in fact, it has already been mastered by hundreds of plants and animals that produce coatings to shed water—these are called hydrophobic coatings. Some animals’ coatings can even shed plant oils, channel water in specific directions and perform a variety of other feats.
Such coatings could be just as useful in the human world. They could prevent windshields, cargo ships, solar panels and smartphones from being fouled by ice, barnacles, snow and peanut butter and enable you to pour every last drop of your expensive makeup from the bottle, among countless other uses.
But Tuteja has found that a coating must be more than just repellent to stand up to the real world. It must be versatile, durable, excellent at repelling, and perhaps most importantly, extremely inexpensive. Getting the right mix of traits has proven to be an enduring challenge.
“It’s not difficult to go into the lab and produce a coating that repels one specific substance from another, but the real world generally doesn’t work that way,” he explains. “On a cargo ship hull, for example, you’re fighting fouling from a great many things – algae, ice, barnacles. And different foulants need to be repelled in different ways. Even substances that seem similar, like snow and ice, require very different strategies.”
To produce coatings that get the job done, Tuteja’s lab has moved away from one-off concoctions and instead focused on producing a library of different repellent properties and how they work. Low surface adhesion, for example, enables foulants to slide off small areas easily, but its effectiveness goes down as surface area increases. Low interfacial toughness, on the other hand, relies not on slipperiness but instead encourages cracks to form between a surface and unwanted crud, encouraging it to slide off even large areas.
Specific insights into exactly what’s happening and why, he says, make it possible to dial up or down specific traits for specific applications—for example, to optimize the balance between low surface adhesion and low interfacial toughness to create a coating that repels ice from both small and large surfaces.
“There needs to be an understanding of the physics behind the problem, the mechanics of what is happening. Why is the material showing the property that it’s showing?” he said. “If we can understand that, we can work to improve the properties we want, or we can find other materials that are likely to produce similar results.”
Tuteja has also learned to pick and choose applications that are less cost-sensitive. A bottle of high-priced makeup is an example of an application where a non-stick coating is a negligible portion of the finished item’s cost. He’s also working on drug delivery systems that dissolve in very specific ways inside the body to release different medications at different times, and on coatings that enable wind turbines to shed ice.
“Years ago, we worked on applications like food packaging, but in those applications, manufacturers often aren’t willing to pay more than about one cent per square meter of coating, even if it works twice as well as what they’re using currently.”
Tutuja is working directly with manufacturers to bring ideas to market, sometimes working directly through U-M and other times through Hygratek, his U-M spinout company created with assistance from the U-M Office of Technology Transfer. He’s currently building pilot-scale coating manufacturing lines and doing extensive wind turbine and solar-array testing in the field, among other ventures.
“Every single project going on in the lab needs to have real-world, tangible applications,” he said. “To me as an engineer, that’s what it has always been about.”