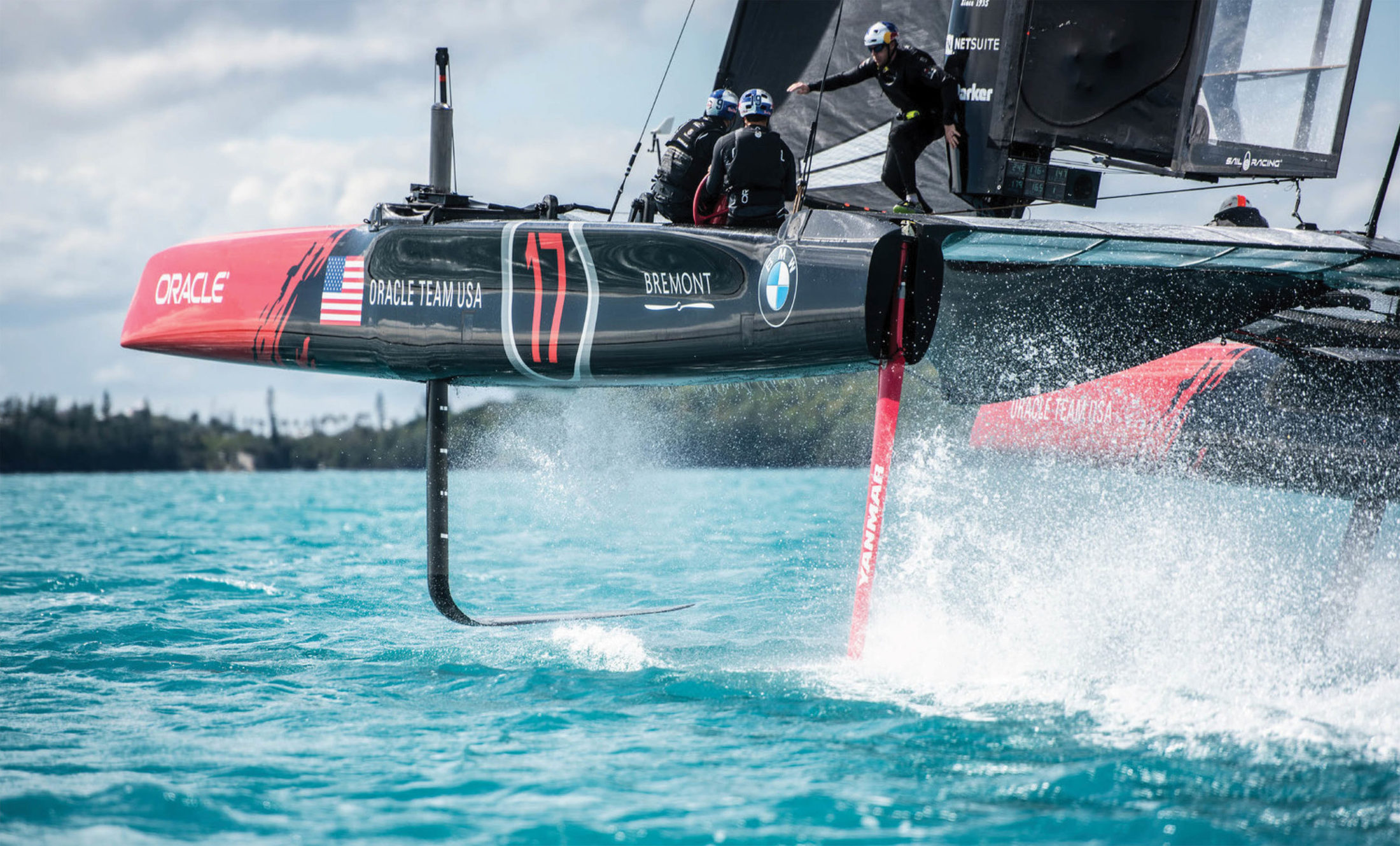
Racing for Control
Flying on hydrofoils means more speed and more risk for the America’s Cup. With the boats and technology moving faster than ever, can these Michigan alumni help their team find the engineering solutions it needs to win in 2017?
Flying on hydrofoils means more speed and more risk for the America’s Cup. With the boats and technology moving faster than ever, can these Michigan alumni help their team find the engineering solutions it needs to win in 2017?
Bermuda’s tropical palette has been flattened to a monochromatic hue. For days, a lingering tropical depression has tormented ORACLE TEAM USA’s rigorous practice schedule. Despite a steady drizzle and feeble winds, the official call is made and the rigging crew begins to mount the 84-foot, rigid-wing sail. Quiet anticipation quickly morphs into organized commotion. The sailors and support team of engineers prepare for a day of testing and fine-tuning components of their competition catamarans. With the next America’s Cup on the horizon and final design deadlines only weeks away, each day on the water is critical for the two-time defending champions.
The technology and teams have become so competitive that a mere one percent advantage in speed is enough to win. Secretive experimentation and creative problem-solving are a must in this battle. In the last America’s Cup, using hydrofoils was allowed for the first time, which spawned a space race in foil development and control. The hydrofoils act as underwater wings that lift the hulls out of the water, practically eliminating drag – and introducing unprecedented speeds. It’s a high-stakes engineering challenge where millions of dollars and the crew’s safety are on the line.
For testing, the crew sails an AC45 – a slightly smaller and simplified version of the 50-footer they’ll race in the June 2017 America’s Cup. Its sleek carbon-fiber body looks more spacecraft than sailboat and is networked with advanced sensors – including the kind used by missiles and other systems that require high-precision navigation. It’s one of three such machines used to do iterative testing of key components. Scott Ferguson (BSE NAME ’85) and Bryan Baker (BSE NAME ’03), both senior members of ORACLE TEAM USA’s engineering team, hold on as their chase boat splashes along in pursuit. Its dashboard is covered with digital monitors featuring live telemetry data streaming from the practice vessel.
“We’ve probably made 90 percent of the boat geometry and systems decisions,” says Ferguson, design team manager. “Now we’re into the fine-tuning and final preparations. The daggerfoils are some of the last things and biggest decisions as far as performance goes.” Today the team is testing the latest version of a daggerboard design as well as new techniques for trimming the rigid-wing sail.
The wind picks up and the crew trims the wing to catch it. Splashing forward, the hulls gain speed until suddenly they’re no longer touching the surface. There’s no more splashing, no more wake. Almost magically, the six-man crew levitates above the waves – balancing the 45-footer on its submerged hydrofoil wings.
The risk factor and additional expense associated with racing on hydrofoils was a controversial decision for the historically traditional sport. Drastically faster speeds and the associated risk have redefined the America’s Cup, widening its appeal to the X Games generation. It’s also ushered in a new era of technology and engineering. “You take a 45-foot object, lift it out of the water and you ride it around on something that’s about the size of a surfboard, says Baker.
Flying these catamarans is like balancing on a unicycle at 50 mph.
Bryan Baker, ORACLE TEAM USA
“Now we’re sailing upwind in a boat that’s half the length at three times the speed,” says Ferguson. “In the past, with big monohulls, we faced a completely different engineering design challenge – which was pretty frightening when it comes to loads and gear, to be honest. Back then, our iterative testing was looking at tenths of knots. Now our design adjustments can make half-knot incremental improvements. It’s been a huge evolution.”
Before foiling was introduced, America’s Cup yachts topped out around 23 knots or roughly 26 mph. In comparison, one of ORACLE TEAM USA’s AC45s reached 52 mph during testing. An object moving through the air encounters one thousand times less drag than one moving through water. The hydrofoils being used in this America’s Cup campaign are seamless, rigid extensions that curve laterally off the bottom of daggerboards – the vertical appendages that extend into the water below the hulls. This hybrid component is referred to as the daggerfoil. The foil shape creates lift in the water using the same principles that allow an airplane to fly through the air. Flight control is not only imperative for the safety of the crew, but it’s also what helps win the race.
Predating the Civil War and modern Olympics, the yachts that race for sailing’s most prestigious trophy, the America’s Cup, have evolved over 165 years. For decades, traits remained familiar to the average sailor: narrow decks, fabric sails and hulls that splashed through the sea at predictable speeds. Then in 2011, a radical mutation in that evolutionary chain occurred. As teams prepared for the last America’s Cup, New Zealand did something unprecedented by equipping its 72-foot catamaran with hydrofoils.
“Once that was discovered, we followed suit quickly and managed to engineer our boat to foil well and still be legal,” says Ferguson. “We won the 2013 cup, barely.”
The successful application of foils to the 72-footers provoked a collective reevaluation as to what was possible. The sport launched into a rapid technological arms race. International teams of engineers began working in isolated unison to solve new problems. Their calculations and designs have led to new ways of moving massive objects across the water at higher speeds, and with the humans on board unharmed.
Hydrofoils have been used on engine-powered ferryboats for decades. Steady thrust from an engine and heavy V-shaped foils makes this type of flying much more predictable and easy to control. In 2009, an experimental hydrofoiling sailboat, Hydroptère, set a sailing speed record by sustaining more than 60 mph for more than 500 meters. However, Hydroptère was designed for speed, lacking the maneuverability and versatility to race up and downwind, between competitors and around buoys.
More recently, smaller Moth-class sailboats and even surfboards have been fit with user-friendly foils. On some foiling Moths, for example, a rod on the bow senses the ride height and makes appropriate trim adjustments on the daggerboard.
“America’s Cup rules prohibit any kind of automated feedback or controls on the yachts,” explains Baker. “You’re not allowed to sense and then have the controls work to those senses. There’s no place for the mechanical feedback of a wand-controlled flap, like on a Moth. The helmsman and crew are in control of the whole thing.”
These constraints have forced teams to innovate and experiment with new foil shapes and materials. The resulting components, and how they’re controlled, are the team’s most highly safeguarded secrets. The thin hydrofoils can resist more pressure than those exerted on the wings of a fighter jet. Micro-adjustments in design and control impact lateral, vertical and heave stability – all of which add up to controlled flight, not nose-diving or launching.
From an engineering and design perspective, it’s opened up a whole new avenue of dynamics. In traditional sailing, height was never a variable. Boats played by the rules of hydrostatics and buoyancy. Flying relatively lightweight catamarans requires different solutions to contend with the extreme side forces against the sail. “If you fly too high, you start to go sideways, and if you fly too high too quickly, you can literally pop out of the water or go sideways really quickly,” says Baker.
Stable, controlled flight on the water is not easy. Crews fight to keep the craft soaring at an optimal height – only a few feet above the waterline. This balancing act is in constant flux as helmsmen jockey for position amidst unpredictable waves and wind. It’s a fine line between speed and stability. “On paper, you can design some really fast foils, but when you go out and race them, they’re really hard to control,” warns Baker.
With only one second warning, a two-meter thick wall of water washes over the bow at nearly 50 mph.
“It’s like concrete,” says Tom Slingsby, ORACLE TEAM USA’S tactician and sailing team manager. “When you have a big splashdown, we often call them a ‘stuff.’ It’s when you get something a little wrong. It happens all the time in testing when you’re pushing right to the limit. We had a big stuff two days ago as we were going through a maneuver and we washed out the rudders that steer the boat.”
It’s a consequence that has come with the speed of flying on foils. “We have a phenomena that happens in the water which is called cavitation, and we have ventilation occur,” explains Baker. It usually occurs when a liquid is subjected to rapid changes of pressure that cause the formation of cavities where the pressure is relatively low. From the sailor’s perspective, a visual cue is when a sheet of air bubbles envelops the submerged foils. When that happens, it’s no longer creating flow through the water and loses all its lift characteristics. The boat comes down fast.
“Probably the scariest and most dangerous scenario is when this happens on the daggerfoil and the wind keeps pushing the wing forward – causing the boat to go bow down,” explains Baker. It’s like the wings being chopped off an airplane.
Sailors wear helmets and protective padding. They’re also now equipped with portable air canisters, since the death of Artemis Racing crew member Andrew Simpson in the last America’s Cup campaign.
“We’re always thinking about safety,” says Baker. “There are openings in the cockpit where the guys can get low and brace themselves. All the guys are wearing oxygen in case the boat capsizes and they get caught up in the rigging and trapped under water. We have a diver that’s on full time. You take on the risk for sure, but that’s engineering. You sweat out the details. You worry about it. You want to push the limits to achieve your goals, but you don’t want to hurt anybody.”
The risk is shared by the engineers and the six man crew.
“If someone gets injured on your watch, it’s not a good feeling, and I’ve had that happen to me in the past,” says Slingsby. When it comes to a splashdown “as soon as you know, you yell out ‘Get down and hold on!’”
Although there’s more danger to deal with, racing in this technological era does have its advantages.
In the 160-year-old dockyard warehouse that the team’s nearly 20 engineers and designers call home, a massive array of digital screens is the backdrop for technical debriefings from the previous day’s performance on the water. These meetings include the engineers, designers and sailors. “We look at all the information we have at our disposal and that usually leads us to a decision,” says Ferguson. “Sometimes we have to rely on a bit of gut feeling, but we also rely heavily on the sailors themselves. They’re on the boat and experiencing things that often lead design directions that we test in the computer. Some things we never would have tested if we didn’t have their input.” Experimenting with foil sections and shapes has come directly from this feedback. When necessary, the team can print some 3D components right on location, others they send abroad to be printed in lightweight metal.
As rapidly as the yachts have evolved, so too has the technology used to design and optimize them. “Our models are getting closer and closer to reality, which allows us to estimate in a very concise way what’s happening on the water,” says Baker.” He continuously compares what’s happening on the water against the team’s theories and simulations.
“I’m using specific geometry algorithms, like neural networks and NURBS topologies, to make a database for the simulations that we run. Then, we tie all that back together and solve a group of equations that figures out how fast the boat will go. Today I’m working through a problem with 19 independent variables – which isn’t even that bad,” jokes Baker.
Going from modeling to testing on the water happens surprisingly fast. “A lot of engineers might go their whole career designing things that never get built,” says Ferguson. “We are the polar opposite to that. We conceive, design, engineer, build and try things in a very short time cycle. It’s a great process that allows us to learn very quickly. It’s one of the things I love most about my job.”
The pursuit of control has led to unprecedented experiments with not only the physical design but also advanced modeling software and control systems. One such experiment included automated systems commonly found in drone technology. In early 2016, through a series of serendipitous connections and recommendations, automated flight expert Ricardo Bencatel was recruited to do something that had never really been done before. At the time, Bencatel was finishing his postdoctoral research at U-M’s Aerospace Engineering Department and had been collaborating on an experimental project with the Italian team, Luna Rossa. However, when the Italians withdrew from the 2017 Cup in response to rule changes, Ricardo and his advisors at Michigan were approached by ORACLE TEAM USA.
Although automated controls are strictly forbidden in actual races, they can be used in interesting ways for experimentation and training purposes. The goal was to see if an automated system could fly the boat better than a manned crew. If so, what could the crew learn from the computer to better prepare for the America’s Cup?
“In the last cup, foiling was new. Just doing it was a big advantage,” says Bencatel. “Now, it’s about refining a way of handling something that’s already known. We’re trying to get some disruptive ideas to give us the advantage.”
This cup, we’re trying to get some disruptive ideas to give us the advantage.
Ricardo Bencatel, ORACLE TEAM USA
The catamarans are covered in sensors that measure a variety of data, like the pitch, flight height and accelerations. That was all fed into Bencatel’s computer model that attempted to optimize the flight by leveling it off to keep it going steady – basically like an autopilot for an airplane, but in a completely different application. In sailing, the wind forces that provide thrust can also tip the boat over. There is a constant balance between what is known as the righting moment and the heeling moment. The side forces against the sail produce the heeling moment. In traditional sailboats, weighted hulls helped counteract these forces and keep the boat upright. With flying catamarans, the heeling moment is counteracted by the rudder and the hydrofoil on the leeward side (the side the wind is pushing to) and the rudder on the windward side (the same side the wind is pushing against). The rudder on the windward side actually creates inverted lift forces – pulling the hull back down into the water and keeping the platform level.
By nature, the AC45 operates under conditions that make it prone to rolling and tipping. An automated control system would have to sense and respond to these forces. The two main components of such a system were already on the boat. The sensors were already there to capture performance analytics. A joystick in the helmsman’s hand controlled the actuators. Bencatel’s mission was to connect the two. Doing so required a tedious programming loop.
He spent most of his time writing code for the controller and its analysis tools. “You go to the water and do tests and tuning,” says Bencatel. “Then you come off the water and you do analysis. And because this is an evolving problem and system, your analytical tools from the previous day are not enough for the new things you want to analyze. So you need to code the analysis tools. If everything goes well, you can identify the issue or bug in the controller code, go back, and correct it. Then you run simulations. And then back to the water.”
“We stuck with reasonably traditional controls in part because of the risk,” says Anouck Girard, Associate Professor of Aerospace Engineering at the University of Michigan and Bencatel’s advisor at the time. “We can try a lot riskier things on a quadrotor in my lab than on a boat that has six humans on board and costs $50 million. We haven’t yet pushed the boundaries of what we know how to do.”
“It’s very similar to aerospace – dealing with air flow, the technology,” says Bencatel. “In practice, the system will do unexpected things. Is that good or bad? Sometimes it’s a better way of controlling the machine than what humans might assume to do.”
One of the most exciting possibilities of the automation work was the possibility to figure out how to foil through turns and other maneuvers.
“I’m frankly amazed with what he’s able to do,” says Ferguson. “It’s not quite like taking your hands off the wheel of a car, but almost.” After months of experimentation, the autopilot was not able to outperform the sailors, and the team was forced to move on due to time constraints. “We learn from things and modify our path,” says Ferguson. “The positive influence he’s had doesn’t change. There are great takeaways from every experiment.” Bencatel stayed on with the team as a control systems analyst.
Everything is speeding up in the pursuit for the America’s Cup, and the fans and teams seem to enjoying the adrenaline.
“There really isn’t a limit to the speeds we can achieve,” says Baker. “We’re pushing it on the structure side, but there’s still more room.”
Unfortunately, there isn’t more time. Design deadlines are only weeks away for the machine ORACLE TEAM USA will fly in June 2017 to defend the America’s Cup. “You begin to realize these are final decisions,” says Ferguson. “In the initial stages, you say ‘Let’s try this and if it doesn’t work we can try something else.’ Now when it comes to decision-making it gets a little bit tense at times.”
That tension reflects the passion that drives the team. In this final phase leading up to the championship race, late nights blend into early mornings and the stakes of each day’s progress grow heavier. “Everybody here wants to succeed at this and win the America’s Cup,” says Baker. “Everybody’s working as hard as they possibly can to achieve that goal.” So are the other competitors, eager to strip ORACLE TEAM USA of its prize; each doing their own secretive experimentation, accelerating the evolution of the sport.
For as much as what’s changed, the spirit remains the same.“Racing has always been about technology,” says Baker. “They go hand in hand. You’re always trying to build a faster something.”
In other words, this is just the beginning. “Seeing these boats fly will inspire the world in unimaginable ways,” says Bencatel.